Industrial Metal Supply Co. is offering its customers the opportunity to dramatically increase their efficiencies using the most advanced 3D 6-Axis laser technology available. Using the FabriGear 300 to cut tube and shapes, customers eliminate multiple manufacturing steps and produce with absolute precision for unsurpassed accuracy and repeatability resulting in consistent quality. The benefit to IMS customers is reduced lead times and higher profits.
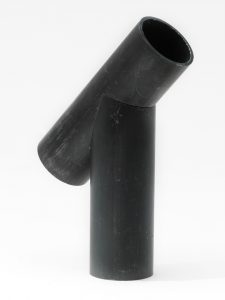
Benefits
- Straight and angled cuts with weld bevels to 45 degrees
- Contoured cuts with weld bevels, tabs and slots
- Drill and tap holes up to ½” in diameter
- Any shape drawn on a CAD system
- Any combination of the above
- Plus, laser engraving for part identification
- Single chucking for lengths up to 26'
- Tighter tolerances and better fit-up for robotic welding
- Eliminate need for tooling and fixturing
- Combine the following into one process:
- Cutting
- Milling
- Drilling
- Tapping
- Coping
- Hand grinding
- Beveling
- Deburring
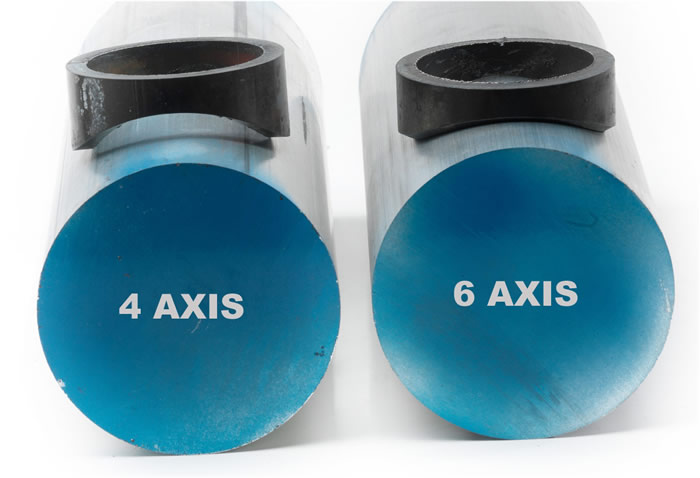
Material
Using the power of a 4000 watt laser it can cut material as long as 26' in length into pieces as short as one inch. The FabriGear 300 works on steel, stainless and aluminum equally well cutting up to:
- 3/4" thick steel
- 1/2" thick stainless steel
- 3/8" aluminum
And, with a robot loading the material, the Fabrigear handles:
- Round tube over 10" in diameter
- Square and rectangle tube up to 8"
- I-beam, channel and structural shapes that fit into an 8" square
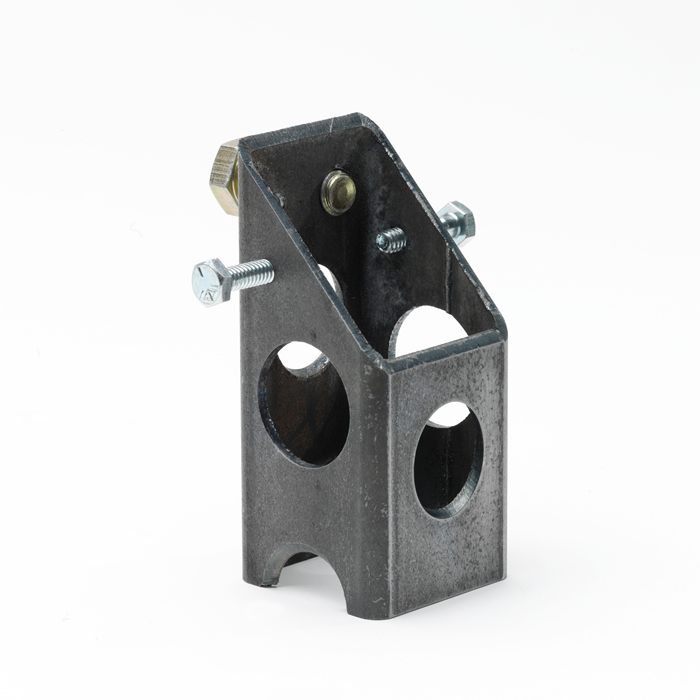
Who Benefits from 3D 6-Axis Laser Cutting?
Fabricators
- Cut parts from shapes and tube including I-beam, channel, T-bar, angle, rectangular tube and pipe
- Bevel or weld chamfer parts
- Drill, end-cut and contour cut tube, pipe or structural parts
- Eliminate manual cutting and measuring operations
- Reduce multiple operations and setups
Machinists
- Cut parts up to 3/4" thick
- Drill and tap holes up to 1/2" near a rounded edge or on multiple sides
- Eliminate fixturing for complex or multi-staged parts
- Reduce multiple operations and setups
- Precision cut parts that are affected by vibrations when machined
- Position cut-outs accurately up to 26' apart in a single chucking
- Precise saddle cuts
- Tab and Slot design can reduce/eliminate the need for fixturing and tooling
- Precut weld bevels for cleaner, more consistent end product
- Precision cuts provide stronger welds using less material
- Space frames and complex tube cuts are now possible without grinding
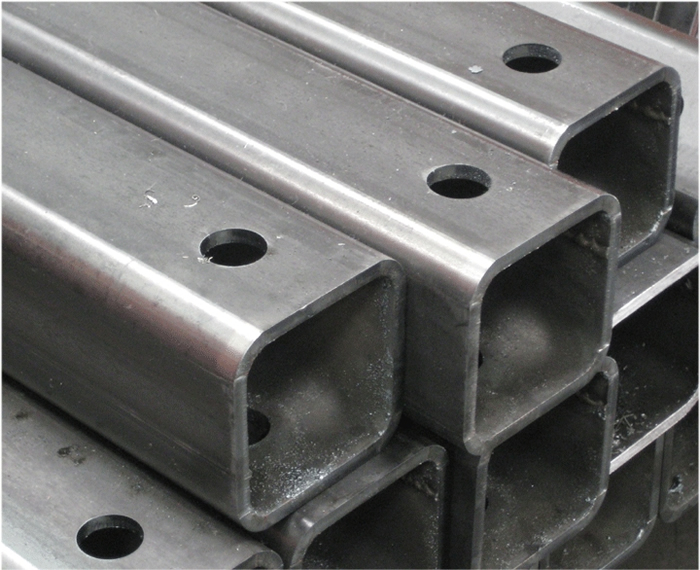
Our Locations
Filter your product specifications, choose product view options,
download our catalog, and create a project list.