Aluminum Custom Extrusions & Metal Contracts
We have very strong partnerships with the top aluminum mills and help many of our customers save time and money by working with the experts to create custom aluminum extrusions. With a custom extrusion, you can use one of the thousands of dies from our mill’s libraries or work with mill experts to create a proprietary die that specifically meets your needs. Our customers have saved thousands of dollars and ample production time by taking advantage of a custom extrusion. By creating a part exactly how you need it, you eliminate material waste and processing labor on areas you would have to mill out otherwise. Why not take advantage of bringing in a mill expert to further extend the quality of your manufactured products? Request a quote here!
An extruded “custom” shape produced to dimensions near the final net dimensions of the finished part. Keeping in mind:
- Extrusion tolerances
- Press capabilities
- Clean-up requirements
- Machine time savings/heavy work load
- Machine tool wear savings
We also are happy to set up metal contracts for those products that you order time and time again. With the metal market pricing being rather volatile why not lock in a price for several months? We’ll also store the material and deliver it to your facility on a scheduled basis – saving you the hassle and cost of having too much metal on your floor at one time.
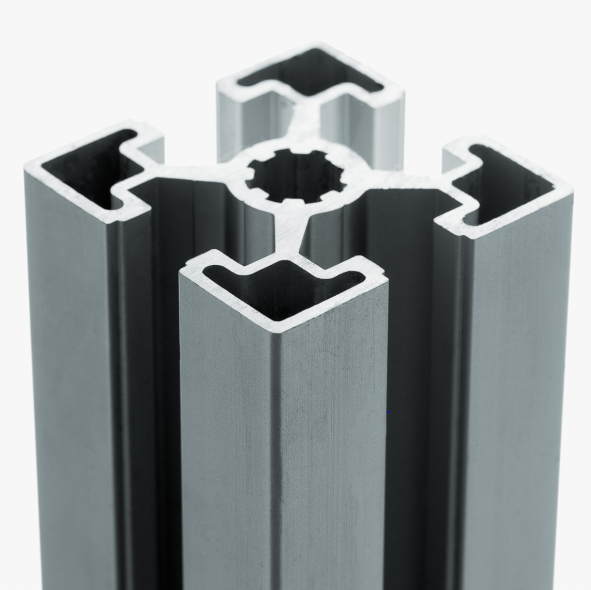
Benefits Of Using Aluminum Extrusions
The AEC (Aluminum Extruders Council) outlines several benefits to utilizing Aluminum Extrusions below.
Aluminum in general and aluminum extrusions, in particular, offer a number of benefits relative to alternative materials and processes.
Aluminum extrusions are:
- Lightweight: Aluminum is about 1/3 the weight of iron, steel, copper or brass, making aluminum extrusions easier to handle, less expensive to ship, and an attractive material for use in applications where weight reduction is a priority such as transportation and other applications involving moving parts.
- Strong: Aluminum extrusions can be made as strong as needed for most applications and, due to the nature of the extrusion process, the strength can be concentrated where it is really needed by including varying wall thicknesses and internal reinforcement in the profile design. Cold-weather applications are particularly well served by extrusions, as aluminum becomes stronger as temperatures fall.
- High in strength-to-weight material: Aluminum extrusions' unique combination of high strength and low weight makes them ideal for applications like aerospace, truck trailer and bridges where load carrying is a key performance.
- Resilient: Aluminum combines strength with flexibility, and can flex under loads or spring back from the shock of impact, leading to the use of extruded components in automotive crash management systems.
- Corrosion resistant: Aluminum extrusions offer excellent corrosion resistance. They do not rust, and the aluminum surface is protected by its own naturally occurring oxide file, a protection that can be enhanced by anodizing or other finishing processes.
- Excellent thermal conductors: Based on weight and overall cost, aluminum conducts heat and cold better than other common metals, making extrusion ideal for applications requiring heat exchangers or heat dissipation. Extrusion's design flexibility allows designers to optimize heat dissipation in housings and other components.
- Non-sparking: Because aluminum is non-sparking, aluminum extrusions are well suited for applications involving explosive materials or taking place in highly flammable environments.
- Excellent electrical conductors: Pound-for-pound, aluminum is twice as conductive as copper, making extrusion a cost-effective alternative for electrical connectors and bus bar distribution components.
- Non-magnetic: As aluminum will not acquire a magnetic charge, extrusions are useful in high-voltage applications and in electronics, where magnetic fields come into play.
- Noncombustible & Nontoxic: Aluminum does not burn and even at extremely high temperatures does not produce toxic fumes.
- Reflective: Surface treatments can produce high reflectance on aluminum components, making aluminum extrusion attractive for lighting applications or for applications where it is desirable to shield areas from light, radio waves or infrared radiation.
- Seamless: Complex shapes can be realized in one-piece extruded aluminum sections without having to rely on mechanical joining. The resultant profile is typically stronger than a comparable assembly, and less likely to loosen or leak over time.
- Easily tailored: While there are a variety of standard extrusion profiles available, the ability to design a profile to meet specific functional, aesthetic, and manufacturability objectives makes aluminum extrusions a preferred element in many product solutions.
- Quick-to-market: Tooling for aluminum extrusion is relatively inexpensive (see material comparisons) with generally short lead times, facilitating prototype development, testing, and product launch.
- Easy to fabricate & assemble: Effective design of aluminum extrusions can greatly simplify subsequent fabrication and assembly, and there are a wide variety of fabrication processes that are routinely employed in the production of extrusion-based components and assemblies.
- Sustainable: Aluminum can be recycled infinitely with no degradation in properties, and aluminum extrusions are often produced with high recycled content — without compromise to aesthetics or functionality. Further, extrusions' inherent properties of light weight, strength, and design flexibility leads to significant in-use benefit to the environment.
Our Locations
Filter your product specifications, choose product view options,
download our catalog, and create a project list.